The Lungs of the Electric Revolution: Lithium Ion Battery Manufacturing
Scaling up lithium ion battery production brings challenges to reach lofty capacity goals. We breakdown the lithium ion battery manufacturing process.
The giant 'gigafactories' that are being built to supply batteries for electric vehicles and energy storage are like massive lungs, breathing life into the electric revolution. However, scaling up battery manufacturing is not as simple as building a bigger factory. Despite rapid improvements in lithium ion battery performance and cost for consumer electronics, efficiently manufacturing lithium ion batteries at the massive gigafactory scale has seen lagging efficiencies and productivity gains. The complex manufacturing processes that produce lithium ion cells have not scaled up as easily as the flagship products they power, creating challenges in the quest to make lithium ion batteries widely affordable and practical for the electric future.
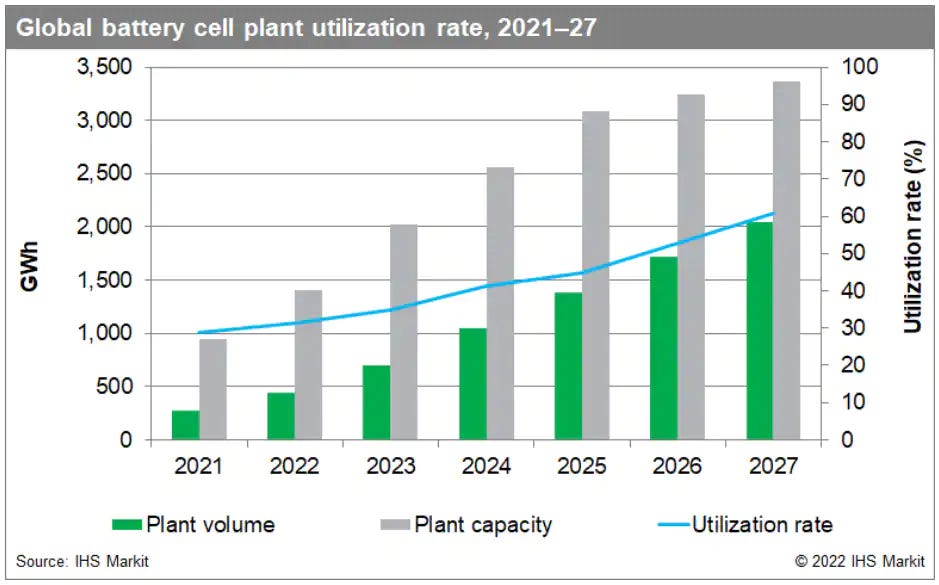
A key metric for manufacturing efficiency is the utilization rate, which refers to how close a factory is to producing at its maximum capacity. Despite unbridled demand, current lithium ion gigafactories have utilization rates around 40% (see figure above), meaning they are not producing batteries nearly as fast or as cheaply as their massive size would suggest. In comparison, modern semiconductor foundries, which also manufacture highly complex products, achieve utilization rates around 80%. The lower utilization of lithium ion gigafactories points to the challenges of scaling up complex battery manufacturing and filling these giant factories with efficient, optimized processes. Unless significant improvements can be made, the under-utilization of gigafactories threatens to slow the expansion of affordable lithium ion batteries and restrain the growth of electrified transportation and renewable energy.
This is the second post in our series on Gigafactories. Checkout our initial post for worldwide exploration into the electric revolution.
The Lithium Ion Battery Manufacturing Process
Lithium ion batteries have revolutionized the consumer electronics industry, enabling smartphones, laptops, and other devices to have long battery life in a lightweight and compact package. However, as lithium ion batteries have been scaled up and adopted for larger applications like electric vehicles, the manufacturing processes have had to evolve significantly. What began as relatively simple electrode coating and cell assembly processes for small batteries have transformed to produce new cathode chemistries and larger cell formats that can power electric cars and store energy for power grids. And although EV battery manufacturers have different cell designs including cylindrical (Panasonic), pouch (LGES, SK On), and prismatic (Samsung SDI, CATL), the cell manufacturing processes are largely the same.
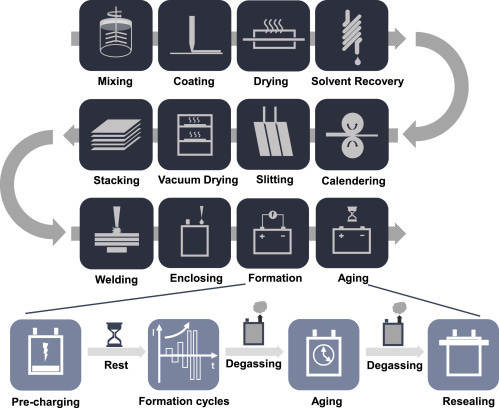
The manufacturing process for lithium ion batteries can be broadly divided into three main stages:
Electrode preparation: The positive and negative electrodes are prepared by coating metal foils with a slurry of active materials, binders, and conductive additives, then drying and compressing the electrodes.
Cell assembly: The electrodes are assembled into battery cells with separators and electrolyte added. The cells are packaged to prevent leakage and allow for connections between cells.
Battery electrochemistry activation: The battery goes through an initial charge and discharge cycle called formation to activate the electrochemistry. The battery then undergoes an aging process to stabilize performance before final testing and packaging.
The folks at BatteryBits provide an exceptional overview of the electrode preparation processes at CATL. They take us through each process step from mixing to slitting with incredible visuals along the way. Unfortunately, there has yet to be a part two of the overview. In the coming weeks, we will bring to life each process step as described by the often cited papers below.
Current and future lithium-ion battery manufacturing, April 2021
Opportunities for the State-of-the-Art Production of LIB Electrodes—A Review, March 2021
Electrode manufacturing for lithium-ion batteries—Analysis of current and next generation processing, July 2019
The goal of this series is provide companies and researchers an updated baseline on the work being done to optimize each part of the current manufacturing process and provide a cross-pollination of ideas. We will then provide a survey of companies who are completely rethinking how gigafactories breathe life into batteries. It is only through manufacturing innovation will the capacity forecast be met.