The Defense Industrial Base Readies Response to the Ukraine Crisis
European countries and the United States ready the defense industrial base in response to the Ukrainian crisis. Cyber intrusions disrupt semiconductor and automotive companies.
Assembly Line
U.S. Military To 3D Print Its Way Out Of Supply Chain Woes
Date: February 27, 2022
Author: Carolyn Schwaar
Vertical: Defense
Tweet | Pocket | Instapaper
Additive manufacturing enables the military to produce new products quickly and cost-effectively, on-demand and at the point of need, either at base, at sea, or on the frontlines. It bolsters the lifespan of legacy systems and vehicles that might otherwise be retired.
Read more at Forbes
Army wants to help industry shore up ‘risk’ in their supply chains
Date: March 1, 2022
Author: Andrew Eversden
Tweet | Pocket | Instapaper
Timothy Goddette, deputy assistant secretary of the Army for acquisition, logistics and technology, said the Army would release interim policy guidance in the third quarter of fiscal 2022 aimed at mitigating supply chain risk alongside industry.
“My message to you all is I think the government needs to help you not manage your supply chain, but we have to have discussions about where the risk is so that we can help where we can help,” Goddette told an audience at the National Defense Industrial Association’s Tactical Wheeled Vehicle conference.
Read more at Breaking Defense
Ukraine to receive 1 million rounds of ammo from Wisconsin factory
Germany’s defence industry transformed by Scholz’s €100bn response to Ukraine crisis
Date: March 1, 2022
Authors: Joe Miller, Erika Solomon
Tweet | Pocket | Instapaper
Germany’s defence industry awakes. Between plans to supply ammunition and tents, lead times for new artillery and vehicles were discussed. This is all happening against a backdrop of how to also handle energy needs for industry throughout Germany.
Read more at Financial Times (Paid)
Implied Poor Russian Army Truck Maintenance

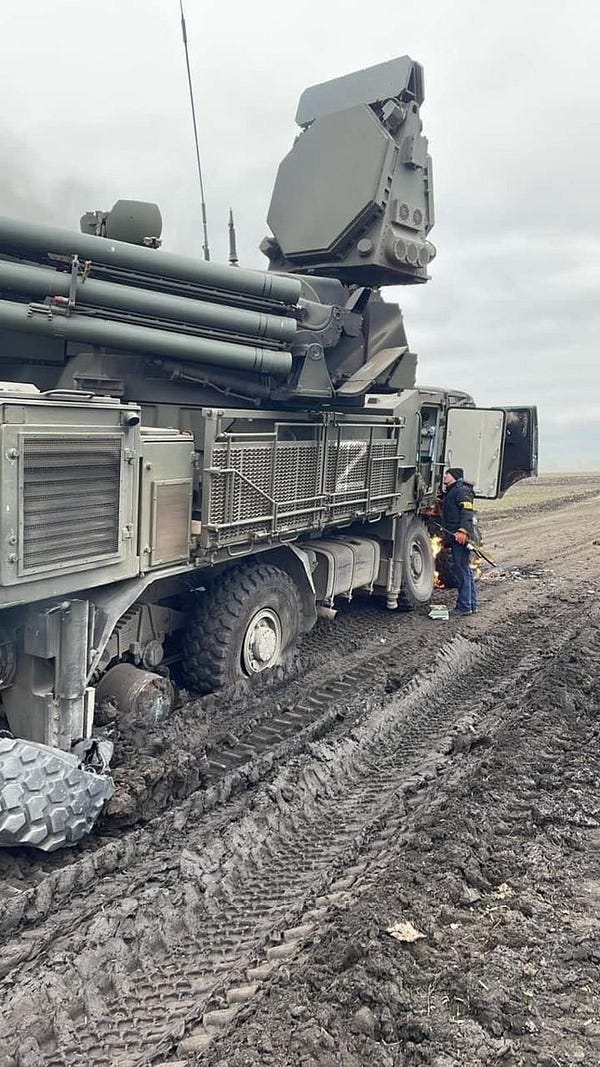
Smart factories drive Korea SMEs to reshore overseas plants
Date: March 3, 2022
Authors: Dae-Kyu Ahn, Gyeong-Jin Min
Tweet | Pocket | Instapaper
The digitalized facility cut production costs by an average of 15.5%, raising productivity and quality by 28.5% and 42.5%, respectively, according to the Ministry of SMEs and Startups. Companies with the plants added 2.6 employees on average and reduced industrial accidents by 6.2%.
“It is urgent to increase productivity per capita by upgrading to smart factories since the falling working-age population is weakening the manufacturing sector’s competitiveness in the mid to long term,” said Noh Min-sun, a research fellow at the Korea Small Business Institute. Local SMEs see the system as a solution to cope with risks from the global supply disruption, the COVID-19, surging commodity prices.
Read more at Korea Economic Daily
Sensors: Data for next-gen composites manufacturing
Date: March 1, 2022
Author: Ginger Gardiner
Tweet | Pocket | Instapaper
Suppliers of dielectric sensors such as Lambient Technologies (Cambridge, Mass., U.S.), Netzsch (Selb, Germany) and Synthesites (Uccle, Belgium) have also demonstrated their ability to shorten cycle times. Synthesites reported from R&D projects with composites manufacturers Hutchinson (Paris, France) and Bombardier Belfast, now Spirit AeroSystems (Belfast, Ireland), that it was able to reduce the cure cycle for RTM6 by 30-50% based on real-time measurements of resin electrical resistance and temperature, which are converted into estimated viscosity and Tg by its Optimold data acquisition unit and Optiview software. “The manufacturer can see the Tg in real time, so they can decide when to stop the cure cycle,” explains Synthesites director Nikos Pantelelis. “They don’t have to wait to complete a longer-than-necessary legacy cycle. For example, the legacy cycle for RTM6 is 2 hours at 180°C for full cure. We’ve seen that in certain geometries this can go down to 70 minutes.”
Read more at CompositesWorld
Nonlinear Static Analysis: Snap-Fit Assembly
Date: March 4, 2022
Author: Nur Ozturk
Tweet | Pocket | Instapaper
Cloud-native engineering simulation enables engineers to test the structural performance and structural integrity of their designs earlier and with accuracy. Advanced solvers that account for thermal and structural behavior can be accessed to provide robust assessments of deformation, stresses, and other design critical output quantities. In this article, we analyze the structural performance and integrity of a casing snap-fit assembly using cloud-native nonlinear static analysis. The focus of this analysis was to detect the peak stress regions, and therefore better understand the likelihood of permanent deformations. After analyzing the structural behavior, the design goal was to ensure safe snap operations, while minimizing the material yielding.
Read more at SimScale Blog
Surge Demand
Google’s AI learns to annotate proteins while Facebook embarks on a new journey to build AI for an embodied interactive metaverse. Automakers are hit hard by supplier cyberattacks and supply chain disruptions within Ukraine. Gecko Robotics raises $73 million to inspect, protect, and efficiently maintain critical infrastructure. Small warehouses begin to automate with success.