Showing the Receipts of Smart Manufacturing
Showing the receipts of Rockwell Automation's "8th Annual State of Smart Manufacturing Report" with proof points of technology adoption for greater resiliency, agility, and sustainability.
We touched on Rockwell Automation’s 8th Annual State of Smart Manufacturing Report in our weekly digest two weeks ago. The report surveyed over a thousand manufacturers across 13 of the top manufacturing countries providing an excellent summary of the technology adoption within manufacturers. Being only a survey, there are no proof points attached. However, here at Exponential Industry, we have been collecting the receipts of smart manufacturing technology adoption.
Exponential Industry began in 2021 to reduce the noise in finding relevant high-value examples for smart manufacturing technology. As part of our curated weekly digest, each use case is tagged with relevant organizations, verticals, and topics to provide focused real-world examples for industry practitioners and investors. In this post, we will explore the top industry verticals and technologies that surfaced in the report.
Why is smart manufacturing adoption accelerating?
Manufacturers are increasingly adopting smart manufacturing technologies to improve their businesses today, primarily due to the need for greater agility and resilience in an ever-changing global landscape. The COVID-19 pandemic has exposed vulnerabilities in supply chains, with widespread disruptions forcing businesses to reevaluate their reliance on traditional manufacturing strategies. Moreover, rising geopolitical tensions have created an uncertain environment, emphasizing the need for flexibility and adaptability. These challenges have created a backdrop for accelerating digital transformation in the manufacturing sector, as companies recognize the importance of incorporating advanced technologies like AI, IIoT, and automation to mitigate risks, optimize processes, and enhance supply chain visibility. By embracing smart manufacturing, industrial businesses can effectively respond to sudden changes in demand, minimize disruptions, and ensure continuity, ultimately strengthening their position in the market and future-proofing their operations.
And as Rockwell’s report puts it:
Manufacturers are turning to technology to tackle the risks that exist both inside and outside the organization. The top two ways respondents are addressing internal risk are to adopt new technology aimed at minimizing disruption from workforce or supply issues (53%) and to shift their operations to the cloud for purposes including increased cybersecurity protection and business continuity (50%). When it comes to external risks like inflation, supply chain, and workforce shortages, the top-ranking mitigation tactic is adopting new technology (44%).
While manufacturers have always sought to future-proof their operations, smart manufacturing technology remains largely new to them due to technology development outside of their industry. Advanced technologies like AI, cloud computing, and augmented reality were largely developed for purposes other than manufacturing and have only recently matured within industrial contexts. This maturity has been driven by several factors:
Technological advancements: Rapid progress in areas such as machine learning, computer vision, and sensor technology has made these advanced technologies more capable, reliable, and efficient and therefore suitable for industrial-grade applications.
Lower costs: The costs of implementing AI, IoT, cloud, and automation technologies have decreased due to economies of scale, increased competition, and technological advancements. This has made these technologies more accessible and affordable to a broader range of businesses, including small and medium-sized enterprises (SMEs).
Interoperability and standardization: The development of industry standards and protocols has facilitated better integration and interoperability among different technologies, systems, and devices. This has made it easier for manufacturers to adopt and deploy smart technologies in their existing infrastructure.
Smart manufacturing uptake depends on the industry unit economics
The traditional unit economics of a manufacturing business involves various factors that contribute to the overall profitability and financial performance. These factors include:
Fixed costs: These are costs that do not change with the level of production, such as rent, machinery, and salaries for certain personnel. Fixed costs can be spread over a larger volume of production, reducing the per-unit cost as production increases.
Variable costs: These costs change with the level of production and include raw materials, labor, and energy. The more units produced, the higher the total variable costs, although economies of scale can lead to a reduction in per-unit variable costs as production increases.
Production volume: The number of units produced directly impacts unit economics, as higher production volumes typically lead to lower per-unit fixed and variable costs due to economies of scale.
Selling price: The price at which a product is sold to customers affects the revenue generated per unit and, in turn, the overall profitability of the manufacturing business.
Gross margin: Gross margin is the difference between the selling price and the cost of goods sold (COGS), which includes both fixed and variable costs. Higher gross margins indicate that a company is more efficient in converting raw materials and labor into finished products.
Manufacturing verticals with higher gross margins typically have more resources to support new operations technology investments. Some of these higher-margin verticals include:
Aerospace and Defense: Manufacturing in the aerospace and defense industry involves the production of high-value, technologically advanced components, and systems. The complexity and precision required in these products, along with long development cycles and high barriers to entry, lead to higher margins that can facilitate investments in advanced manufacturing technologies.
Semiconductors and Electronics: The semiconductor and electronics industry is known for rapid innovation, miniaturization, and technological advancements. The production of these high-value components often requires specialized equipment, cleanroom environments, and precision manufacturing processes. The resulting high margins allow for investments in cutting-edge manufacturing technologies to maintain a competitive edge.
Life Sciences: The production of pharmaceuticals and biotechnology products often involves complex processes, high levels of research and development, and stringent regulatory requirements. These factors contribute to higher margins, which can support investments in new technologies.
It is no surprise that the report confirms these higher-margin verticals devote more of their operating budget to technology investment.
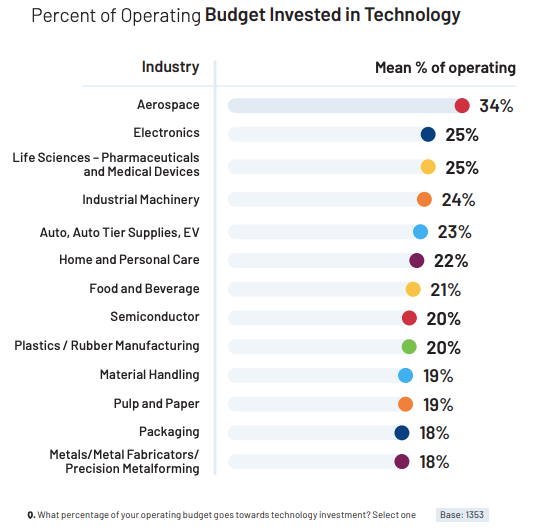
It is only when looking deeper into which smart manufacturing technology investments each vertical prefers does the story get interesting.
Aerospace (34% of operating budget)
The aerospace industry is adopting a broad set of smart manufacturing technologies including additive manufacturing, digital twins, and augmented reality. Additive manufacturing is enabling aerospace manufacturers to reduce the complexity of their assemblies while using lighter and stronger materials. Digital twins and real-time data technologies are used for understanding how aircraft perform throughout their lifecycle and powering new business models. Augmented reality helps assemblers and maintenance technicians improve first-time quality with up-to-date schematics and digital work instructions streamed in real-time into their field of view. Overall, the technology investments in aerospace are spread out over lower production volumes and are focused on improving product performance and reducing lifecycle costs.
Electronics (25%)
The electronics industry is focusing its attention on the automation of assembly and end-of-line testing, advanced analytics, and materials recovery. The assembly and testing of electronics are labor intensive so new automation is being deployed to alleviate the burden. Advanced analytics is improving quality and efficiency in surface-mount technology and hard drive manufacturing. New methods of material recovery are required to combat the proliferation of e-waste and reduce materials costs. Since electronics are high-volume goods, the value of technology investments seeks to minimize variable costs.
Automotive, Auto Suppliers, and Electric Vehicles (23%)
The automotive industry is undergoing a transformation in powertrain technology and autonomy with the rapid adoption of electric vehicles and advanced driver assistance underway. This transformation has some OEMs creating full-scale virtual factories in the metaverse (digital twins) to change how automotive assembly facilities are managed over their lifecycles. Also, additive manufacturing and AI technologies are speeding up production ramps. Put together, smart technology bets in the automotive sector center around a dogma that “A High Production Rate Solves Many Ills.”
The rest of the verticals
The rest of the manufacturing verticals have their own story. Explore the Life Sciences (25%), Industrial Machinery (24%), Food & Beverage (21%), Semiconductor (20%), Plastics, Rubber, Chemical (20%), Pulp and Paper (19%), Primary Metal & Fabricated Metal (18%) verticals to see where their technology adoption story leads.
Process automation and cloud/SaaS are the most popular investments
Among all industries, process automation and cloud computing technologies are the most widely adopted. Our receipts indicate two major reasons that are applicable to every manufacturing vertical:
Cost savings: Both process automation and cloud computing technologies are proven to reduce operational costs. Process automation reduces labor costs by automating repetitive tasks, minimizing human errors, and increasing overall efficiency. Cloud computing enables manufacturers to eliminate the need for expensive on-premise infrastructure and move to a more cost-effective pay-as-you-go model, reducing IT costs and maintenance expenses.
Improved efficiency and productivity: Process automation streamlines production workflows, reduces cycle times, and increases throughput, leading to overall productivity improvements. Cloud computing enables real-time data access and analysis, improving decision-making and facilitating faster responses to production issues or market changes.
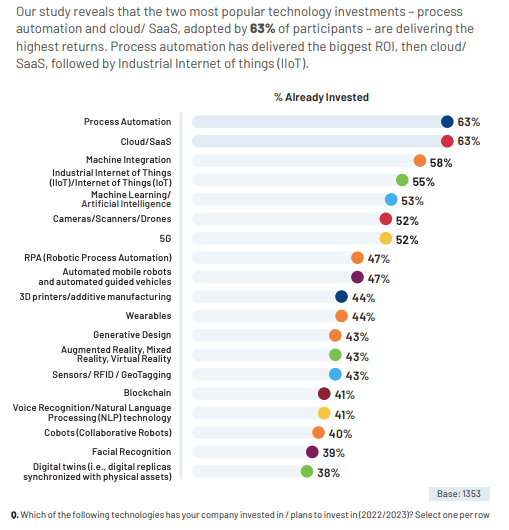
The Exponential Industry topic pages cover the gamut of the rest of the popular investments. Explore the topics you are most interested in using the links below.
Process Automation
Cloud Computing and SaaS
Machine Integration
AI and Machine Learning
Cameras/Scanners/Drones
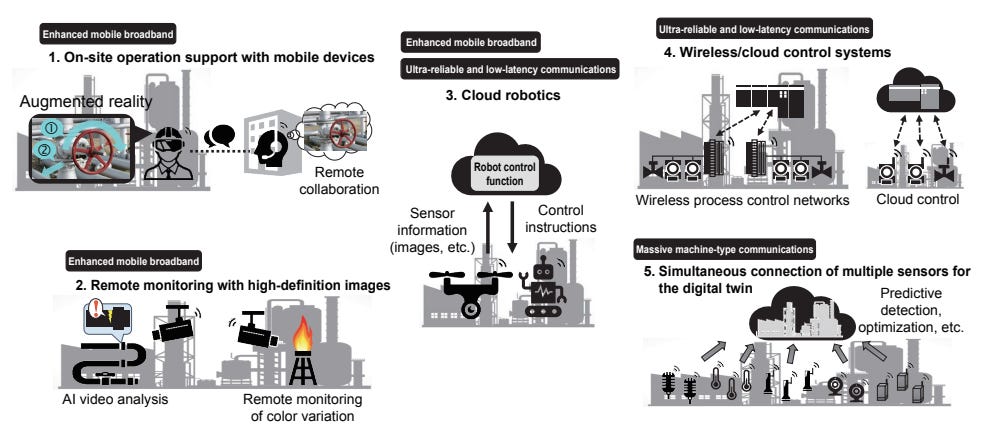
Augmented Reality (AR) & Virtual Reality (VR)
Embracing the Promising Future of Smart Manufacturing
As the global market becomes more interconnected despite geopolitical uncertainty and the pace of technological innovation accelerates, the adoption of smart manufacturing will become increasingly essential for businesses to maintain their competitive edge. Furthermore, the growing focus on sustainability and circular economy principles will push manufacturers to invest in smart technologies that minimize waste, conserve resources, and reduce environmental impact.
In the future, we can expect to see even more sophisticated and interconnected smart manufacturing ecosystems, with greater collaboration between machines, humans, and systems. The emergence of Industry 4.0 and the continued development of advanced technologies will drive further transformation, enabling new levels of efficiency, customization, and innovation in the manufacturing sector. Embracing smart manufacturing will be crucial for businesses to navigate the challenges and opportunities of the 2020s and secure their place in the rapidly evolving global economy.
Thanks for reading, next week we will continue our blog series on Lithium Ion Battery Manufacturing.