Material Impact: LK-99 Manufacturing is Not Guaranteed
Powdered metal defects' impact on Pratt-Whitney jet engines and graphene scale-up show a hard road ahead for producing advanced superconducting material LK-99.
A week before the LK-99 craze took hold, another material had a material impact on RTX (fka Raytheon) to the tune of $13 billion in market value.
According to an earnings report, the company described a manufacturing-quality issue due to contamination in the powdered metal used in their state-of-the-art jet turbine engines.
Chris Calio, chief operating officer, said the issue is that the powdered metal used to produce certain engine parts may reduce the life of those parts. The metal has been used in Pratt’s products for decades, but the company has determined that the contamination was present in rare instances in metal produced from roughly the fourth quarter of 2015 into the third quarter of 2021.
Beyond the initial 200 engines to be removed, Pratt is expecting that about 1,000 additional PW1100 engines will be removed for enhanced inspection.
Calio said it was a manufacturing-quality issue that was first uncovered in 2020 when there was an incident with a V2500 turbine disk that turned out to be the result of a rare contamination in the metal. The company immediately inspected the entire V2500 fleet and reviewed the powdered-metal process, among other safety measures.
Days later their main turbine engine competitor, CFM International (owned by Safran and GE Aerospace), reportedly “discovered a quality issue related to powdered metal at an unnamed supplier in 2021, and has fully implemented repairs.”
Powder metallurgy has a long history dating back to the iron age. The conventional process has not changed much in the centuries since, but humans have been able to create hotter furnaces enabling more specialized metal alloys.
Aerospace companies like RTX and GE Aerospace use metal powder to create high-performance super-alloys that can better resist the intense heat inside an operating jet engine. If a jet engine component is defective due to contaminants within the powered metallurgy process, the strength of the part could be significantly weakened and result in unexpected and potentially catastrophic outcomes.
Advanced materials, such as the alloys used in jet engines, are behind some of the greatest products we have ever made. LK-99 has a chance to be the next great material. However, harnessing it in a lab and scaling it up into a controlled industrial process is HARD.
Manufacturing High Strength Parts with Powered Metallurgy
The powdered metallurgy process is relatively simple:
Metals are powdered through solid-state reduction, atomization, electrolysis, or chemical treatments like oxide reduction and thermal decomposition.
Powders are mixed with other metals, alloying agents, and lubricants to reduce friction and increase fluidity while yielding a homogeneous mix that will be fed into a rigid toolset for processing.
The metal blend is compacted into the appropriate geometry using dies, punches, hydraulic presses, or other consolidation measures.
Compacted pieces are sintered in a controlled atmosphere using extremely high temperatures to metallurgically bond the particulates.
Parts are subjected to secondary operations depending on the requirements of their final application.
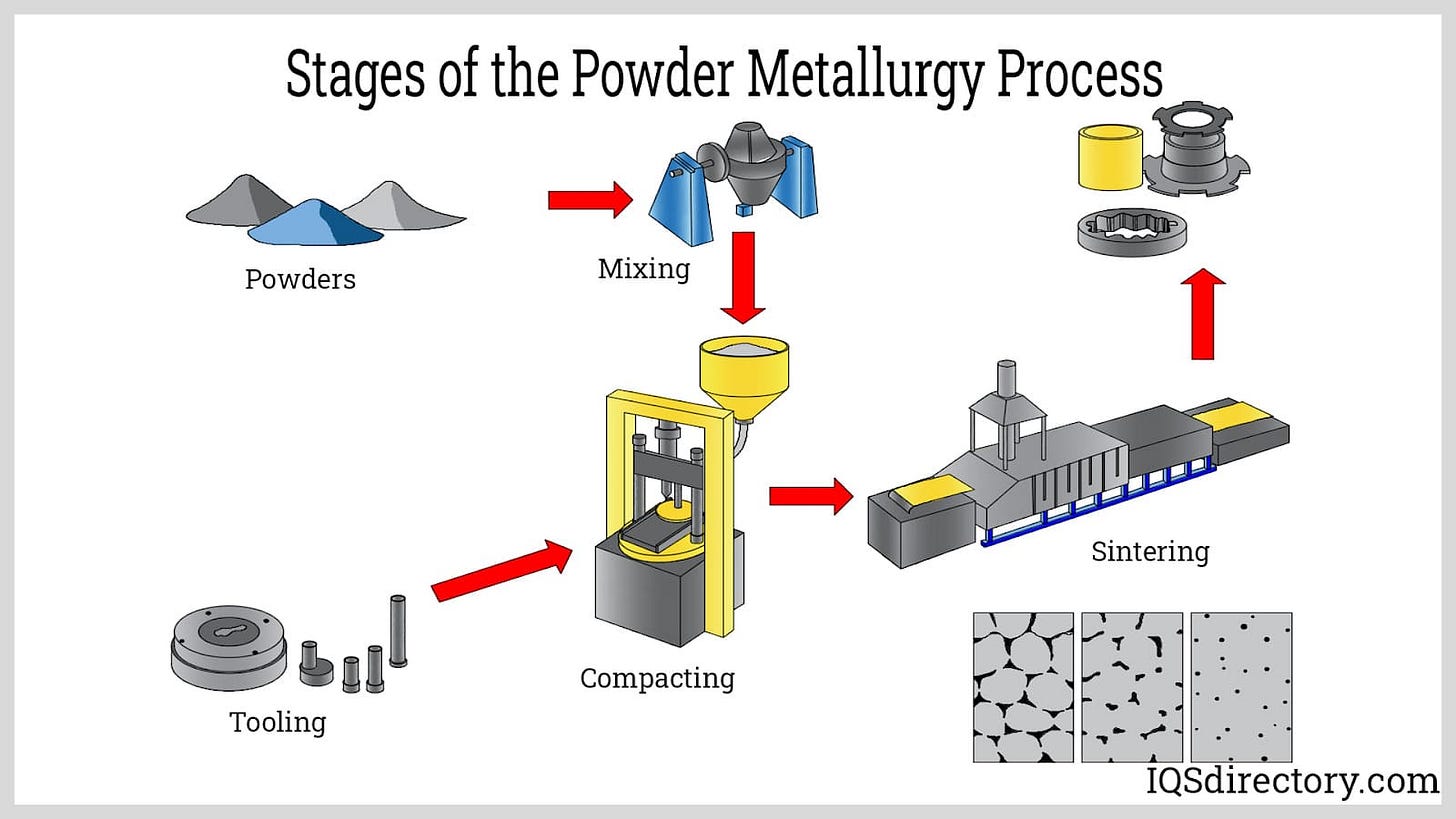
Powdered metal parts provide many advantages that improve part quality and uniformity, shorten production times, and cut down project costs over other manufacturing methods. Allowing for extensive customization and providing repetitive accuracy, powdered metal parts are appropriate for various applications.
LK-99 Production Process Stages
While LK-99 is not a metal, it’s a ceramic, the patented manufacturing method involves similar simplicity of steps. The Wired story on Andrew McCalip, an engineer at Varda Space, succinctly describes the process:
Making LK-99 is not quite garage science, but it is a relatively simple alchemy. The El Segundo, California, lab of Varda Space Industries, the satellite startup where McCalip is an engineer, happens to contain the appropriate furnaces, vacuum systems, and environmental chambers. All that McCalip would require was four ingredients: red phosphorus and copper to synthesize copper phosphide, and lead sulfate and lead oxide to make a mineral called lanarkite. Those two materials would then be pulverized, mixed, blasted with heat, and cooled, producing something that’s close to another familiar compound—lead apatite—but in which some lead atoms have been swapped out for copper.
That should sound very familiar to the powered metallurgy described above, but manufacturing an advanced material is never that straightforward. Graphene, another promising material in the world of superconductivity, has many incredible physical properties that arise from its one-atom-thick carbon structure. However, it remains difficult to manufacture at an industrial scale but it’s still worthwhile to be used in certain valuable industrial processes.
As of late 2022, Ford Motor Co., is one of the only companies to use graphene at industrial scales. Starting in 2018, Ford began making plastic for its vehicles that are 0.5% graphene – increasing the plastic’s strength by 20%.
The academic community remains skeptical that LK-99 is truly a room-temperature superconductor and can be reproduced. However, Dr. Sinéad Griffin of the Lawrence Berkeley National Laboratory simulated the electron structure, and the results suggest conduction pathways for electrons are in just the right conditions and places that would enable them to ‘superconduct.’ But, “these interesting conduction pathways only form when the copper atom percolates into the less likely location in the crystal lattice, or the ‘higher energy’ binding site. This means the LK-99 material is difficult to synthesize since only a small fraction of crystal gets its copper in just the right location.”
It is not surprising that researchers around the world are struggling to reproduce the LK-99 finding. The ability to synthesize the material a second time has taken over 20 years since it was first discovered in 1999. We are now at the slow grind of lab reproduction. Just look at the set of initial questions Andrew McCalip had on his attempts to reproduce:
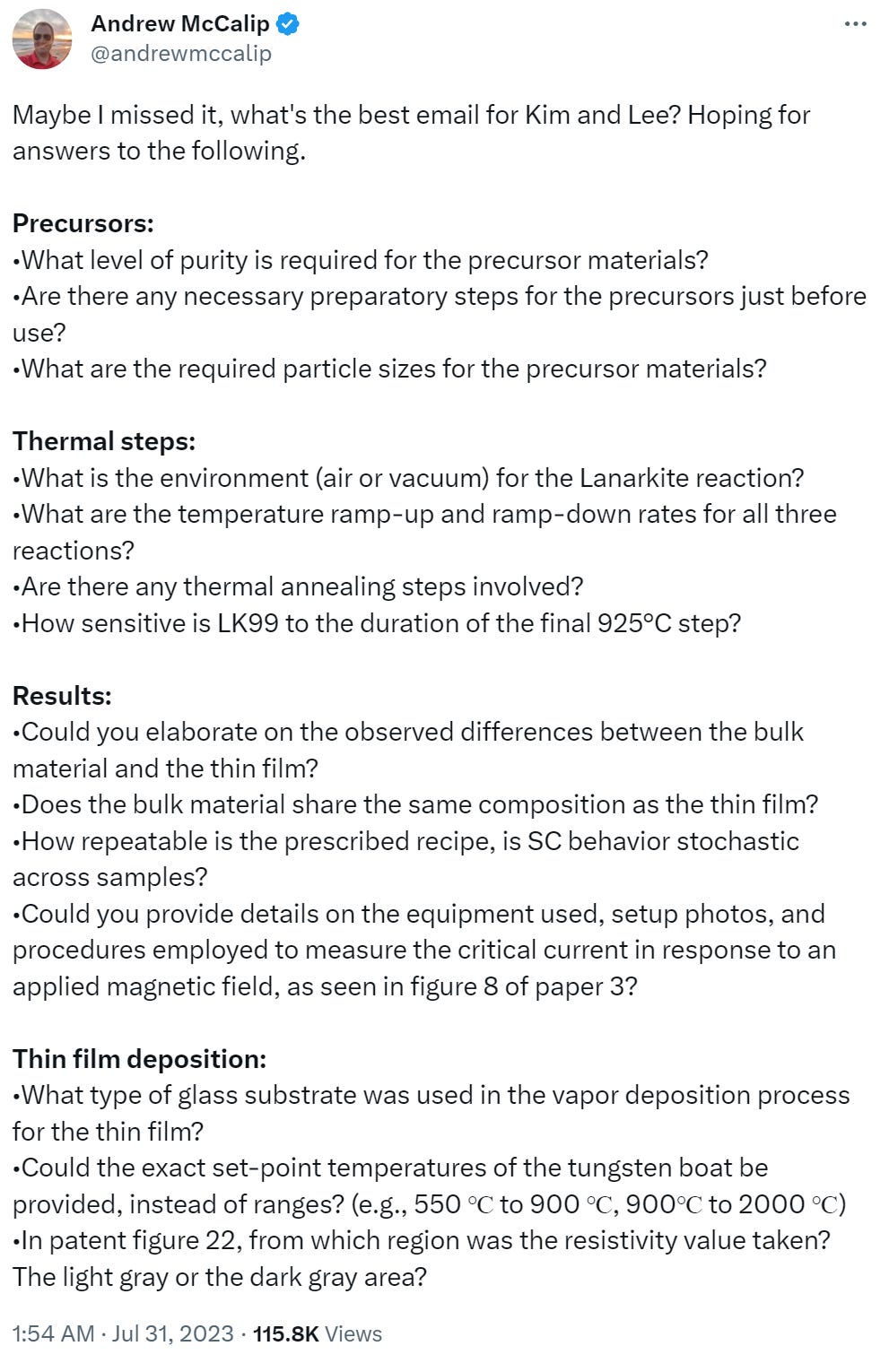
As with graphene, even if we are able to reproducibly synthesize LK-99 in a lab it will take years before we are able to synthesize it with sufficient yield due to how precise the resulting electron structure needs to be.
Manufacturing Advanced Materials is Hard
In the intricate realm of materials science and manufacturing, even well-established processes like the powdered metal process for jet engine components, are not immune to unforeseen challenges. Contamination, even in minute quantities, can drastically alter the properties of materials, rendering them unsuitable for their intended applications. Such incidents underscore the importance of rigorous quality control and continuous monitoring in manufacturing. Even a slight deviation can have cascading effects, compromising not only the material's integrity but also the safety and reliability of the products they constitute. As the demand for advanced materials grows, so does the need for meticulous oversight in their production to ensure that they consistently meet the highest standards of quality and performance.
Novel materials, like LK-99 and graphene, despite their groundbreaking potential, often face a challenging journey from laboratory discovery to industrial-scale production. The initial excitement surrounding a new material's unique properties in a controlled lab environment is just the beginning. Transitioning to industrial-scale production requires extensive testing, optimization, and adaptation of manufacturing processes. Factors such as cost-effectiveness, scalability, and reproducibility become paramount. Additionally, the material's performance under varied real-world conditions, its long-term stability, and potential environmental or safety concerns must be thoroughly evaluated. Even with promising initial results, many materials face technical and economic hurdles that can delay or even halt their transition to the market. Thus, while the discovery of LK-99 is a significant milestone, its journey from the lab bench to industrial application will be a rigorous and lengthy endeavor.