Inline Measurement Creates Opportunity in Factories
New automation for optimizing liquid mixing, steel making, and shot peening advances with inline measurement. Demystifying the history of industrial revolutions.
Assembly Line
Fingerprinting liquids for composites
Date: January 18, 2022
Tweet | Pocket | Instapaper
Collo uses electromagnetic sensors and edge analytics to optimize resin degassing, mixing, infusion, polymerization and cure as well as monitoring drift from benchmarked process parameters and enabling in-situ process control.
“So, the solution we are offering is real-time, inline measurement directly from the process,” says Järveläinen. “Our system then converts that data into physical quantities that are understandable and actionable, like rheological viscosity, and it helps to ensure high-quality liquid processes and products. It also allows optimizing the processes. For example, you can shorten mixing time because you can clearly see when mixing is complete. So, you can improve productivity, save energy and reduce scrap versus less optimized processing.”
Read more at Composites World
AI-based operational excellence in steel manufacturing
Date: January 20, 2022
Author: Shreebhooshan B
Vertical: Primary Metal
Tweet | Pocket | Instapaper
Modern steelmaking is heavily instrumented with several process parameters being monitored, yet there are limited operational insights available in real-time. Take, for instance, the continuous casting process − a facility producing 150 tonnes per hour can generate over US$5 million per day in production revenue, assuming current steel prices. Conversely, a single day of lost production is equivalent to US$5 million worth of losses. Therefore, a manufacturer can unlock tremendous value by eliminating these unscheduled production downtimes.
Casting molten steel, unsurprisingly, is hard on heavy equipment. Components wear under harsh conditions leading to failures or adverse product quality. Early detection of such conditions could warn the maintenance and production managers to schedule repairs before failures occur. Applying advanced analytics to machine and process data can help in predicting such unwanted events. Data-science projects are often designed for specific use cases thereby limiting the scope and interoperability of the model. The approach faces challenges in terms of model sustenance in production and scalability across use-cases or plants.
Read more at Falkonry Blog
Industrial Automation for Spraying and Shot Peening
Date: January 20, 2022
Tweet | Pocket | Instapaper
Spraying and shot peening are processes used to increase the life span of metal parts in machinery. This procedure is commonly used in the aerospace and marine industry where metal structures need to cope with harsh environmental conditions. As companies try to maximise profits, industrial automation for spraying and shot peening that helps minimise repair costs have gained popularity.
The Augmentus Platform eliminates the need for coding and robot teaching even for complex surface treatment applications. Our technology allows users to accurately 3D scan parts and automatically generate optimized robot path planning. Therefore, companies are able to easily and rapidly deploy robots without the need for robotic experts, even in a high-mix production environment.
Read more at Augmentus Blog
Building The Future Show - Jonah Myerberg Co-Founder and CTO at Desktop Metal
Collaborative Robotics in Manufacturing Assembly
Date: January 18, 2022
Tweet | Pocket | Instapaper
Assembling transformed materials into components is a key step in the manufacturing process. Due to growing product complexity and variety, there is a need for the design of components that are constructed out of a variety of materials for diverse functional purposes alongside aesthetic value. Moreover, trends in manufacturing and industry are toward mass customization in highly competitive global markets, with assembly a key value-added activity at the end of the supply chain.
Collaborative robots (cobots) are a key development in the field of robotics that show vast potential for multiple industries, including manufacturing. Technologies such as artificial intelligence, machine learning, neural networks, and sensors (such as vision, contact, torque, and force detecting sensors) have given Cobots improved interaction with their environment. This has facilitated a new paradigm in robotics where operators and robots work together to share tasks.
Read more at AZO Materials

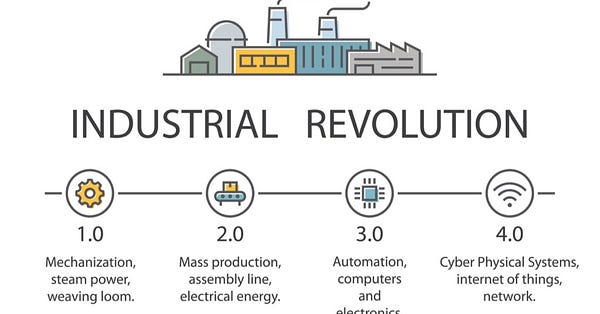
How Drishti empowers deep learning in manufacturing
Date: January 20, 2022
Tweet | Pocket | Instapaper
During his talk at the MLDS Conference, ‘New developments in Deep Learning for unlikely industries’, Shankar outlined Drishti’s industrial applications of AI in manufacturing. The company leverages deep learning and computer vision to automate the analysis of factory floor videos. Essentially, the company has installed cameras on assembly lines that capture videos on which the company runs object detection, anomaly detection and action recognition. Then, the data is sent to industrial engineers to improve the line.
Read more at Analytics India Magazine
Surge Demand
Intel plans the largest silicon manufacturing location on the planet outside Columbus, Ohio while placing orders for ASML’s next-generation EUV lithography machines. BAE Systems and Stanley Black & Decker discuss the factory of the future. The great resignation is affecting the production floor and accelerating digitization efforts. GE Digital names a new CEO.