Electrode Manufacturing: Coating Electrode Material Uniformly
Electrode coating contributes ~15% to the total battery manufacturing cost. Electrode coating techniques are transforming from slot-die to dry calendering and electrostatic spray deposition.
The cost of lithium-ion batteries (LIB) per kWh has dropped exponentially over the past two decades. However, manufacturing remains about 25% of LIB cost with process improvements lagging behind other areas of battery research. Currently, the manufacturing of LIBs is a multi-stage process including slurry mixing, coating, drying, calendering, slitting, vacuum drying, swiss roll fabrication, welding, packaging, electrolyte filling, formation, and aging.” Beyond LIBs, solid-state batteries (SSBs), sodium-ion batteries, lithium-sulfur batteries, lithium-air batteries, and multivalent batteries have been proposed and developed, but LIBs will are currently poised to dominate the market at least for the next decade.
Today, we focus on the electrode coating processes within electrode manufacturing. Check out our initial posts on the World’s Gigafactories, an overview of the Lithium Ion Battery Manufacturing Process, and A Dive into Slurry Mixing. The videos contained within this post series are accessible in our Battery Manufacturing Technology YouTube playlist.
From Batch Mixing to Continuous Flow
Last week, we discussed how an electrode slurry is produced using large-scale industrial mixers. To increase overall process throughput, an ideal electrode slurry would be capable of being coated at high speeds with few defects. In the coating process, the electrode material is transferred onto a metal foil to create uniform electrodes. Aluminum (Al) and copper (Cu) foils are used for positive electrodes and negative electrodes respectively.
In the overall manufacturing system, the coating, drying, and calendering processes are connected together by a roll-to-roll system. Roll-to-roll systems improve life cycle costs and increase the scale of operation, making it a high throughput system. Often, this means the upstream mixing step is a bottleneck in the production line.
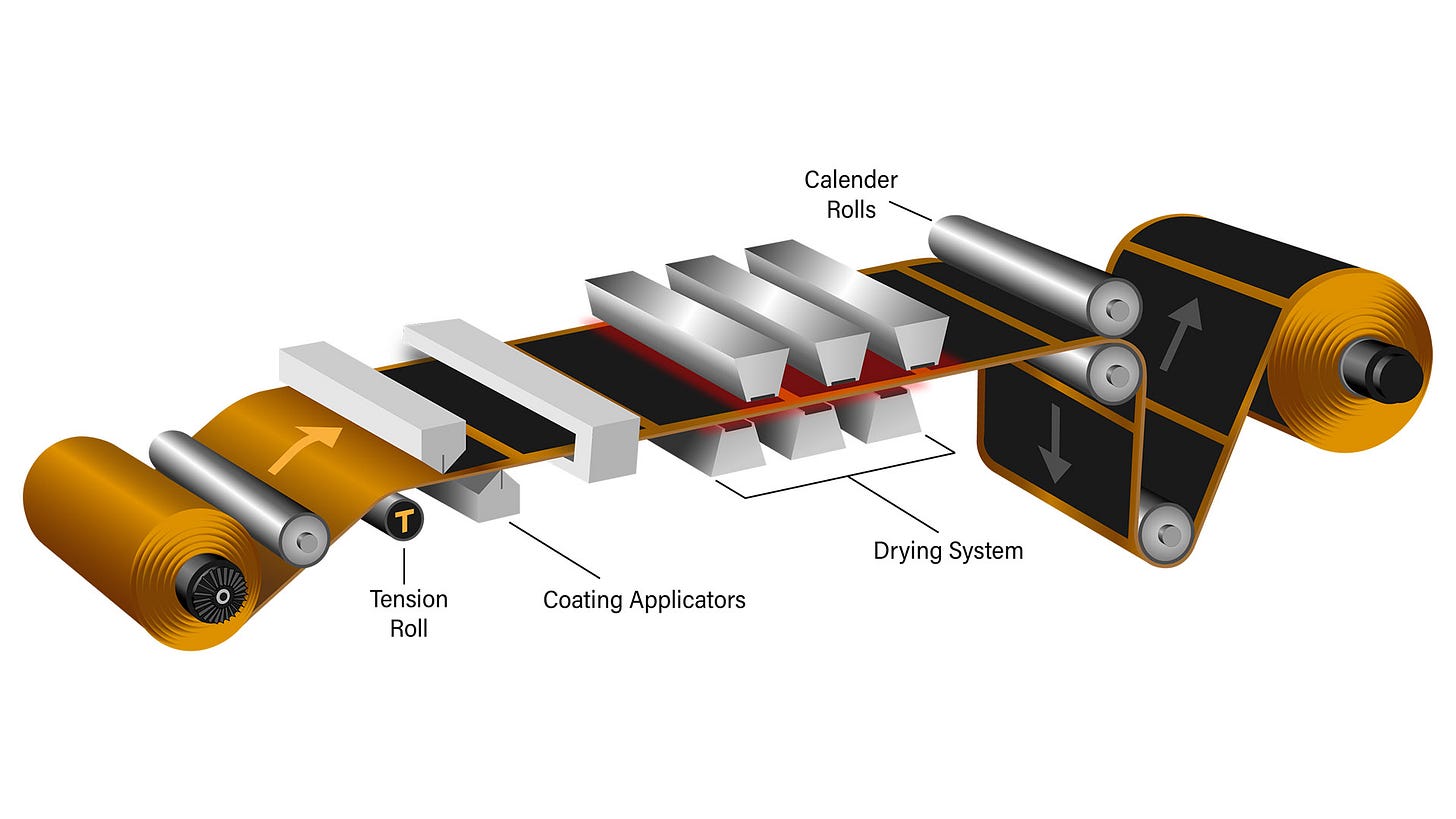
Roll-to-roll materials manufacturing involves continuous processing of a flexible substrate as it is conveyed along a roller-based processing line. The output results in rolls of finished material produced in a cost-effective and efficient manner. Source: National Renewable Energy Laboratory (NREL)
After the coating process, the resultant electrode is passed through a drying oven to evaporate the solvent, leaving behind a solid, continuous electrode layer. Once the electrode is fully dried and cured, it is wound onto a take-up roll to be fed back through the process for the other electrode type (cathode or anode) or to flow directly to calendering (if using a two-sided coater). Solvent recovery systems are employed in the drying process to minimize waste and reduce environmental impact. Dürr describes a roll-to-roll electrode coating, drying, and solvent recovery process in the video below.
Overall, continuous flow roll-to-roll production systems have become the standard in battery electrode manufacturing due to their scalability, uniformity, and cost-effectiveness. While there are some drawbacks, such as initial investment costs and waste generation, the benefits generally outweigh these concerns in high-volume production scenarios.
Electrode Coating Techniques
The coating process involves the application of an electrode material onto a substrate, which is then dried and cured to form a solid, continuous electrode layer. Three popular electrode coating techniques include slot-die coating, dry electrode coating, and electrostatic spray deposition. Only Slot-die coating utilizes an aqueous slurry mix, the other two techniques use dry materials.
Slot-Die Coating via Low Solvent Content Extrusion
Low solvent content extrusion is a method that involves the use of a highly viscous coating slurry with low solvent content. The process involves passing the slurry through an extrusion die, which forms a uniform and continuous coating on the collector. On a lab scale, the coating is usually achieved with relatively primitive equipment such as the doctor blade, while at the industrial level, the state-of-the-art is the slot die coater.
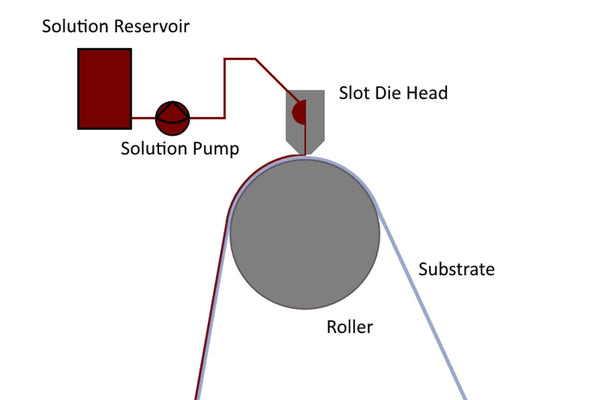
Slot-die coating is the dominant coating technique in electrode manufacturing today. In this technique, the electrode slurry is delivered through a narrow slot onto the moving substrate. The slot is designed to provide a uniform, continuous flow of slurry, ensuring a consistent coating thickness across the entire width of the substrate. In the video below, Tapemark engineer Mike Rothaupt explains what slot die coating is and the benefits of the technique.
Key Attributes
Throughput: Slot-die coating offers high throughput, between 35–80 m/min for electrode manufacturing, due to its continuous nature and compatibility with roll-to-roll systems. The technique can be easily scaled to accommodate various production volumes.
Quality Constraints: The success of slot-die coating relies on the precise control of slurry flow rate, substrate speed, and the gap between the slot and the substrate. Variations in these parameters can lead to non-uniform coatings or defects, influencing battery performance.
Other Performance Indicators: Slot-die coating is a relatively low-waste process, as it only dispenses the required amount of slurry. However, it is more suitable for medium to high-viscosity slurries and may not be appropriate for low-viscosity or highly shear-sensitive materials.
Dry Electrode Coating (Dry Calendering)
Dry electrode coating, also known as dry calendering, involves the direct application of a dry electrode material onto the substrate. This method eliminates the need for a solvent in the electrode slurry, reducing drying times and the environmental impact associated with solvent use and recovery. Dry electrode coating is the Tesla 4680 battery’s secret sauce and is explained in more detail by CEO Elon Musk and SVP Drew Baglino at Tesla Battery Day 2020 in the video below.
Key Attributes
Throughput: Dry electrode coating can offer faster production times due to the absence of a drying step while also being scalable to roll-to-roll production. However, the technique may require specialized equipment and modifications to existing production lines, which can impact throughput.
Quality Constraints: Achieving a uniform and consistent dry electrode coating can be challenging, as the process relies on the precise control of powder distribution and compaction. In addition, the technique may not be suitable for all electrode chemistries and may require the development of new binder materials.
Other Performance Indicators: Dry electrode coating is an environmentally friendly process due to the elimination of solvents. It can also lead to higher energy-density batteries, as the absence of a solvent allows for the use of thicker electrode layers.
Learn more: Hieu Duong, Joon Shin & Yudi Yudi of Maxwell Technologies, bought by Tesla, describe their breakthroughs in “Dry Electrode Coating Technology.” Also, a new dry-coating process developed by the Fraunhofer Institute for Material and Beam Technology IWS, DRYtraec®, is illustrated below.
Electrostatic Coating
Electrostatic coating is a process that involves the deposition of charged electrode material onto a conductive substrate by applying an electric field. The technique used in electrode manufacturing is known as electrostatic spray deposition (ESD). ESD is a process in which the electrode material is atomized into fine droplets and charged electrostatically. The charged droplets are then sprayed onto a grounded substrate, where they adhere and form a uniform coating.
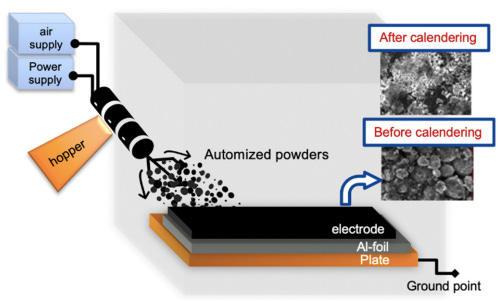
Throughput: ESD is generally a slow process; the fabrication of an 18 mm × 25 mm electrode sheet takes around one minute. However, it can be an ideal choice for small-scale or specialty battery production due to its flexibility and ability to accommodate various electrode materials and thicknesses.
Quality Constraints: Achieving a uniform and consistent coating with ESD can be difficult, as the process is sensitive to factors such as droplet size, charge, and spray distance. Additionally, ESD may be unsuitable for some electrode materials due to their electrical properties or sensitivity to electrostatic charging.
Other Performance Indicators: ESD can be a low-waste process, as excess material can be collected and reused. It also offers greater control over the coating thickness and morphology, which can enhance battery performance.
Summarizing Electrode Coating
Electrode coating is a crucial process in manufacturing batteries and other electronic devices. Roll-to-roll manufacturing techniques are well known for scaling up electrode coating in a cost-effective and high-throughput manner. By transitioning from batch mixing processing to a continuous roll-to-roll process, the coating speed can be increased substantially while maintaining high quality and uniformity. Roll-to-roll methods are also compatible with scaling up the process to wider web widths, enabling extremely high throughput. With continued innovation, dry electrode coating is poised to compete with slot-die coating to meet the demand for batteries and electric vehicles on a global scale.
After coating, wet electrodes go through a drying process requiring significant energy to evaporate the solvent. And while industrial drying can take place in the span of just a few minutes it will take us a week to distill the process for you. See you next week!