Electrode Manufacturing: A Dive into Slurry Mixing
The slurry mixing step contributes ~8% to the total battery manufacturing cost. Examine well-known methods for slurry mixing: hydrodynamic shear mixing, ball-mill mixing, and ultrasonic homogenization
The cost of lithium-ion batteries (LIB) per kWh has dropped exponentially over the past two decades. However, manufacturing remains about 25% of LIB cost with process improvements lagging behind other areas of battery research. Currently, the manufacturing of LIBs is a multi-stage process including slurry mixing, coating, drying, calendering, slitting, vacuum drying, swiss roll fabrication, welding, packaging, electrolyte filling, formation, and aging.” Beyond LIBs, solid-state batteries (SSBs), sodium-ion batteries, lithium-sulfur batteries, lithium-air batteries, and multivalent batteries have been proposed and developed, but LIBs will are currently poised to dominate the market at least for the next decade.
Today, we focus on the slurry mixing manufacturing process. Check out our initial posts on the World’s Gigafactories and an overview of the Lithium Ion Battery Manufacturing Process. The videos contained within this post series are accessible in our Battery Manufacturing Technology YouTube playlist.
The Slurry Mixing Process
Slurry mixing is the first step in the battery manufacturing process. The result of the mixing process is a suspension, referred to as an electrode slurry, that contains the raw material mixture necessary to produce battery electrodes. The slurry mixing process combines active electrode materials, binding agents, and solvents to create a consistent liquid that can then be coated onto thin metal foils to form battery electrodes. Proper slurry mixing is key to evenly dispersing materials, avoiding unwanted chemical reactions, and enabling the slurry to have the correct viscosity for the coating process. The animation below shows the current manufacturing equipment needed to perform slurry mixing at scale.
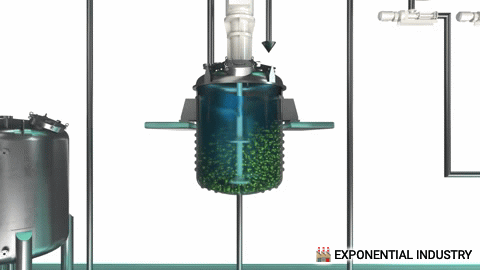
Liu et al. provide a straightforward summary of tradeoffs in designing a mixing process for manufacturing electrode slurry at scale:
The slurry mixing step contributes to 7.9% of the total manufacturing cost, and it takes a relatively long time to get a suitable slurry for the following manufacturing processes. The current industry employs planetary mixers to prepare large-volume slurries for production. The target of modifying mixing technology is to lower the cost by improving the throughput. The electrochemical performance of the electrodes is also highly related to the mixing condition and operation. The mixing uniformity can affect the electrode microstructure and materials distribution (Bockholt et al., 2016)
Furthermore, LG Energy Solutions, a top EV battery maker, describes the components of the slurry mixing process in greater detail in the video below. A viable electrode slurry's two most paramount features are that it is stable and processable with essential properties including rheology (or viscosity), homogeneity, and carbon black (CB) particle agglomeration.
Slurry Mixing & Blending Methods
Three well-known methods exist for mixing: hydrodynamic shear mixing, ball-mill mixing, or ultrasonic homogenization. W. Blake Hawley and Jianlin Li from Oak Ridge National Laboratory describe each approach for slurry mixing with current industrial machinery.
Shear mixers come in many varieties, such as planetary mixers and Rushton turbines, and represent the most common industrial equipment. Energetic ball-mill mixing has been demonstrated to degrade high-MW aqueous binders, meaning it may be a technique best reserved to dry blend active materials and conductive additives. Ultrasonic techniques have become of increasing appeal since they are capable of producing better dispersions at lower energy inputs than shear mixers and are compatible with high-performance conductive additives like carbon nanotubes. However, there are scalability issues associated with ultrasonication, since high-power systems have yet to sufficiently proliferate the intensity of cavitation.
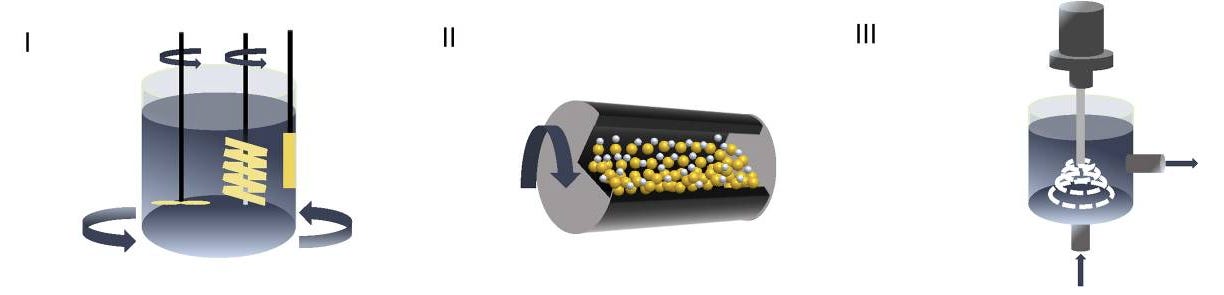
Hydrodynamic Shear Mixing
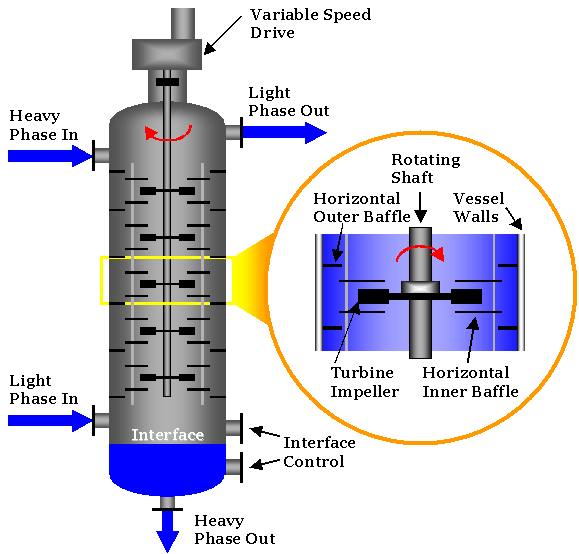
Hydrodynamic shear mixing is the most widely used method in battery manufacturing processes for mixing slurry. It is economical and can be easily scaled up. In this process, the slurry is subjected to high shear forces generated by a high-speed mixer typically configured with a rotating shaft and a Rushton-type turbine. The shear forces break down particle agglomerates and ensure uniform dispersion of the active materials and binder throughout the slurry.
Key manufacturing process parameters for hydrodynamic shear mixing are mixing speed and mixing time.
The impeller design, alignment of the impellers, overall mixer design, and dosing systems can all impact the quality of the slurry produced. Lancaster Products describes some of the design tradeoffs made in their high-shear mixer to increase product material yields.
Ball-Mill Mixing
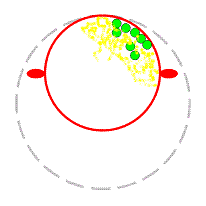
Ball-mill mixing is another common method for slurry mixing. In this process, the slurry components (active materials, binders, and solvents) are mixed together in a rotating container filled with grinding media, such as steel or ceramic balls. The centrifugal forces, created by the rotation of the container around its own axis together with the rotation of the turn disc, are applied to the components and milling balls in the bowl. The balls' high-energy collisions break down the agglomerates and disperse the particles uniformly throughout the slurry.
Key manufacturing process parameters for ball-mill mixing include the ball-to-powder weight ratio, milling speed, and milling time.
Ultrasonic Homogenization

Ultrasonic homogenization mixing is another technique utilized in battery manufacturing for slurry preparation. This method uses high-frequency ultrasonic waves to create pressure changes in the slurry, inducing cavitation. The implosion of cavitation bubbles generates intense local shear forces, which break down particle agglomerates and disperse the components uniformly in the slurry. One major advantage of ultrasonic homogenizers is the low number of wetted and moving parts. This reduces frictional wear and cleaning time.
A key manufacturing process parameter in ultrasonic homogenization mixing is the target percentage of the maximum amplitude setting. The frequency of vibration is typically constant for any given ultrasonic homogenizer.
As far as scaling up ultrasonic homogenization mixers, larger probes behave somewhat differently from smaller ones. The maximum amplitude decreases as the size of a probe increases. This is because it takes more energy to move a larger probe. (See Scaling Up An Ultrasonic Homogenization Process)
Additional Slurry Mixing Manufacturing Considerations
Common defects in battery manufacturing processes associated with slurry preparation include particle agglomeration, insufficient binder dispersion, and non-uniform coating of the active materials. These defects can lead to poor electrochemical performance, reduced cycle life, and safety issues in the final battery product.
Key rheological properties that determine the quality of the slurry include viscosity, thixotropy, and yield stress. These properties are essential for proper slurry flow, coating thickness control, and adhesion to the current collector (more on this next week!).
Quality checks for slurry preparation involve measuring and controlling the slurry's rheological properties, particle size distribution, and solid content. These parameters should be monitored and maintained within the specified ranges to ensure a homogeneous slurry capable of producing high-quality battery electrodes.
When analyzing the quality and yield of an electrode slurry manufacturing process keep in mind the following notes:
The order in which components are added to the suspension is important.
Slurry viscosity must be viewed in the context of shear rate and temperature.
Slurry rheology alone cannot predict electrochemical performance.
Summary of Slurry Mixing for Electrode Manufacturing
In summary, hydrodynamic shear mixing, ball-mill mixing, and ultrasonic homogenization mixing are industrial-scale techniques in battery electrode manufacturing for slurry preparation. These techniques have been borrowed from other manufacturing processes and adapted to electrode preparation. As a result, these mixing techniques are mature in their lifecycle and easily accessible from many vendors driving down the cost of this process step (~8% of battery manufacturing cost). However, optimizing the machine design and process parameters for each method is crucial for achieving a homogeneous slurry with desired rheological properties, which ultimately ensures the production of high-quality battery electrodes with minimal defects.
Dive Deeper into Slurry Mixing
Our battery manufacturing technology YouTube playlist aggregates the best explanations of battery manufacturing technology. Some of the top machine builders include:
Bühler Group offers future-oriented wet mixing, grinding, and dispersing technology solutions for a variety of industries.
Maschinenfabrik Gustav Eirich (Eirich), with its strategic center in Hardheim, is a supplier of machines, plants, and services for mixing technology, granulating/pelletizing, drying, and fine grinding. Their core competencies are processes for the preparation of bulk materials, slurries, and sludges.
Thurne Teknik (Thurne), in cooperation with DEC GROUP offers a large number of solutions to support the battery manufacturing industry in the field of contained powder handling.
Erich NETZSCH (NETZSCH) is a mid-sized family-owned German company engaging in the manufacture of machinery and instrumentation with worldwide production, sales, and service branches.
Rheology of Battery Slurries
Thanks for reading, next week we will investigate the coating process step.