Design for Sustainability, Modularity, and Flexibility
Additive manufacturing is finding its sweet spot in design for sustainability. Factory systems embrace modular design, opening opportunities for machine to machine communication and flexible robots.
Assembly Line
Design for Sustainability
Date: March 9, 2022
Tweet | Pocket | Instapaper
Typically, product designers select a few focuses, for instance, design for manufacturing (DFM), design for assembly (DFA) and design for reliability (DFR), and optimise those aspects of the product. Every design decision is evaluated in the light of the selected focus or focuses and relevant changes are then made taking the full life cycle of the product into account.
A sustainable alternative to this system is the circular economy. The main focus of this type of economic model is to reintroduce used parts as raw materials for new products. The intent is to move from a high-waste to a high-value model. Such a system is highly resource-efficient and reduces the effect of consumer demand on the exploration, pollution, and wastage of natural resources. Models such as biomimicry, cradle-to-cradle, product service systems (PSS), 4Rs, are all strategies that can provide design features to achieve a circular economy.
Read more at Fractory Engineering Blog
How 3D printing improves sustainability across the supply chain
Date: March 9, 2022
Tweet | Pocket | Instapaper
After analyzing several studies about energy efficiency of 3D printing, the answer is not as simple. Due to very individual use cases (machine, product and process characteristics), comparability of traditional methods and 3D printing is not always generally possible. While compared with subtractive methods, 3D printing can be more energy efficient (especially due to lesser material consumption). The energy consumption of 3D printing compared to injection molding is generally considered to be higher due to a way longer production time per part (less than a minute per part for injection molding, several hours for 3D printing). However, other factors such as the energy consumption for producing the mold, the production volume and material efficiency have to be taken into account. When looking into lower volumes, it becomes a fact that additive manufacturing is a more sustainable production method, regarding energy efficiency.
Read more at Replique Blog
Additive Manufacturers Can Learn From Chip Manufacturers

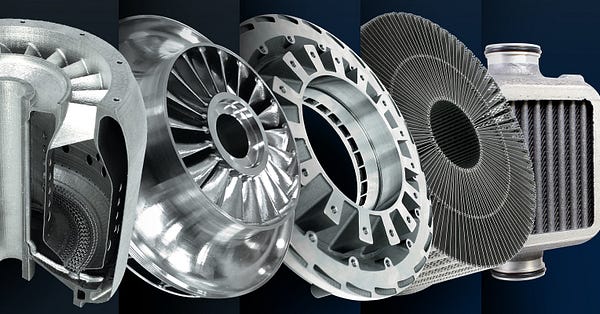
Next to the last steel mill in town, a robotic farm grows backed by Pritzker billions
Date: March 5, 2022
Author: Rebecca Fannin
Vertical: Agriculture
Tweet | Pocket | Instapaper
“Our smart manufacturing facility improves the yield, taste and texture of the vegetables, and does that with 95% less water, 95% less land, and uses no pesticides or chemicals,” said Webb, who is 33. Fifth Season’s automated proprietary system grows fresh produce year-round indoors in vertical trays, relying on artificial intelligence, robotics and data to control light, water and nutrients, and harvest leafy greens.
Fifth Season is competing in a capital intensive, highly fragmented market with more than 2,000, mostly smaller farms and a handful of larger scale players. Among the largest is San Francisco-based Plenty Unlimited, which recently inked $400 million in strategic funding from Walmart and plans to sell its fresh produce from its Compton facility at the retailer’s California stores. Another major rival is AeroFarms in Newark, New Jersey, which scrapped a SPAC deal to go public in October 2021 and is continuing to build out capacity at a Danville, Virginia farm.
Read more at CNBC
Flexible robotic arm put to work with AR
Date: March 7, 2022
Tweet | Pocket | Instapaper
According to Imperial, the flexible arm can twist and turn in all directions, making it customisable for applications in manufacturing, spacecraft maintenance, and injury rehabilitation. In use, people working with the robot would manually bend the arm into the precise shape needed for each task, a level of flexibility made possible by layers of mylar sheets inside, which slide over one another and can lock into place. So far, configuring the robot into specific shapes without guidance has presented challenges.
To enhance the robot’s user-friendliness, researchers at Imperial’s REDS (Robotic manipulation: Engineering, Design, and Science) Lab designed a system for users to see in AR how to configure their robot. Wearing mixed reality smartglasses and through motion tracking cameras, users see templates and designs in front of them superimposed onto their real-world environment. They then adjust the robotic arm until it matches the template, which turns green on successful configuration so that the robot can be locked into place.
Read more at The Manufacturer
Robots Become More Useful In Factories
Date: March 10, 2022
Author: John Koon
Tweet | Pocket | Instapaper
“The main focus of manufacturing is to increase productivity measured in throughput over a time period, with minimum downtime,” said Sathishkumar Balasubramanian, head of product management and marketing for IC verification at Siemens EDA. “But assembly line manufacturing line is a dynamic environment, and automation is only part of the solution. On the outside, it seems to be important to have constant flow. However, variability in manufacturing flow is inevitable, and how the manufacturing process adapts to variation is highly critical to keep the downtime to a minimum. For example, in bottling manufacturing, how the work moves from station 1 to station 4, and a change in bottle orientation, can be addressed by an adaptive production line to meet peak demand with minimum disruption. That is very important. The ability to sense the status of manufacturing line at the edge is key to robotic manufacturing process.”
Read more at Semiconductor Engineering
The Connected Soldier
Manufacturing: Security and Resilience Start with Visibility
Date: March 8, 2022
Author: Heather MacKenzie
Tweet | Pocket | Instapaper
Having real-time situational awareness of your OT networks, including visibility into assets, connections, communications, protocols and more, allows you to start improving cyber resiliency. The good news is that you can automate asset inventory for manufacturing facilities, eliminate blind spots, and reveal assets that might have previously been missed.
Once you’ve got excellent visibility, you can move onto risk reduction. This requires real-time detection of vulnerabilities, threats and anomalies at both brownfield and greenfield facilities. It includes process insights that highlight threats to reliability, such as failing equipment, unusual variable values and networking communication anomalies.
Read more at Nozomi Networks Blog
Metrology Primer
Date: March 6, 2022
Author: Doug Mule
Vertical: Semiconductor
Tweet | Pocket | Instapaper
The cost of defect failures is starting to spiral out of control, and the cheapest insurance against this is more Metrology and Inspection. One of the changes the industry is adopting is advanced packaging as the primary driver to increasing semiconductor performance. The push to advanced packaging has an entire set of consequences, namely newer packaging technology and a new vector of failure.
Additionally, Metrology and Inspection spending tends to ramp before the rest of the tools, and that is why they should continue to grow so robustly in 2022 given that large fabs are just starting to come online. Metrology and inspection ramps are likely happening currently for the N3 and N5 nodes at TSMC and Intel.
Read more at Fabricated Knowledge
Make the Most of MES
Date: March 7, 2022
Author: Jim Camillo
Tweet | Pocket | Instapaper
MES software is by no means a new tool for manufacturing, having been around since the mid-1980s. However, for various reasons, manufacturers of all sizes in all industries often don’t take full advantage of the software’s capabilities. New benefits like scalability, affordability, low-code programming and traceability, complement traditional ones like error-proofing and optimizing workflow.
Miklosey says some end-users increasingly prefer using MES systems that prioritize baseline and scalable business intelligence (BI) analysis. These systems let companies access the software’s terabytes of native data with no need for third-party integration. Insights from this data help manufacturers be more responsive to their customers’ needs. FactoryLogix, for example, is readily accessible by the manufacturer’s BI platform of choice.
Meeting the IPC’s Connected Factory Exchange (CFX) standard in MES is another challenge being addressed by software suppliers. Aegis greatly contributed to the development of the CFX, which emphasizes plug-and-play connections to simplify machine-to-machine communication, analogous to USB computer devices.
Read more at Assembly Magazine
Computer-on-Modules For Autonomous Intralogistics Vehicles
Date: March 9, 2022
Tweet | Pocket | Instapaper
At Transpharm Logistik, however, the promotional products change frequently and come in different shapes, sizes and weights. Staff therefore have to pick them individually per recipient. Nevertheless, Transpharm Supply Chain Analyst Martin Zwiebel was tasked to optimize the pick and delivery process further. “Staff were using heavy, bulky carts to pick promotional products,” recounts Zwiebel. Equipped with tablets and supported in some cases by pick-by-light systems, they gathered the individual items from across the entire warehouse and then wheeled the cart with the complete pick to the packing department, where the promotional products were made ready for dispatch. “When looking for a faster and easier solution, it became apparent that a driverless transport system promised significant advantages,” the analyst continued. So, what was needed was an affordable robotic trolley that could autonomously find its way to the next storage bay following a predefined optimized route, and that would prove a constant and helpful companion to staff.
Read more at Robotics Tomorrow
CNC builders look to software, machine-health data, customization and modular design
Date: March 9, 2022
Author: Anna Townshend
Tweet | Pocket | Instapaper
The adoption of on-machine components follows the development of more and more sophisticated hardware and software for better machine-to-machine communication. Increasingly, components are using multiple protocols, facilitating deeper communication for easier access to more in-depth data. Customers of systems integrators like Methods Machine Tools want solutions for faster and more specific data collection from any protocol, in order to boost production with predictive maintenance insight.
“The emergence of data as a tool to enable real-time decision making on the shop floor is evolving how companies run and maintain their machines,” Parenteau says. Whereas old alarms signaled the presence of an issue, detailed diagnostics can instead tell operators precisely what the issue is. For example, rather than just letting an operator know how much cutting fluid is in the tank of a CNC machine, more advanced on-machine components could tell someone the viscosity and temperature of the fluid. That information can be used to improve machining processes and resolve minor issues before they become costly problems. Coolant flow is another variable that is closely monitored in CNC machine tools, as it can have a direct impact on shop productivity or part quality, he says.
Read more at Control Design