3D Nano Desktop Stratasystems
You could take any two big 3D printing companies you could find plenty of business overlap because it’s such a small world.
It all started with a meme. Reflecting on 3D Systems’ ‘Superior Proposal’ to combine with Stratasys on May 30th, Duann Scott from Bits to Atoms did a bit of memeing on LinkedIn.
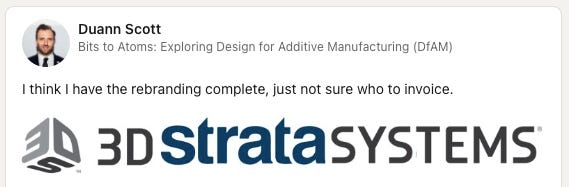
However, I don’t think Duann went far enough. Nano Dimension has pestered Stratasys for months (starting in March) while maintaining a 14.2% stake in the company. Ultimately, Stratasys continued to reject Nano Dimension and proceeded to formally announce an all-stock transaction with Desktop Metal valued at approximately $1.8 billion the week before 3D Systems submitted their offer.

Therefore, I propose 3D Nano Desktop Stratasystems to describe the whole brouhaha. But there’s plenty more to the 3D-printer manufacturer saga.
A Short History Of The Aforementioned 3D Printer Manufacturers
In 1986, Charles "Chuck" Hull was granted a patent for his stereolithography system, and his company, 3D Systems Corporation was formed and launched the first commercial 3D printer, the SLA-1 in 1988. Also originating in 1988, S. Scott Crump co-founded his company Stratasys which marketed its first fused deposition modeling (FDM) machine in 1992.
As 3DInsider puts it, if we take 3D printing from its origin to the present day, it will look something like this:
The Infancy Stage: 1981 to 1999
The Adolescence Stage: 1999 to 2010
The Adult Stage: 2011 to the present day
Picking up in the post-global financial crisis adult stage, venture capital investment in 3D printing startups began to pour in across the globe. Nano Dimension (2012, Israel) and Desktop Metal (2015, Cambridge, USA) both got their start during the early innings of this stage. Stratasys even contributed to Desktop Metal’s Series A funding round in 2015. Overall, venture investors remain attracted to 3D printer manufacturers’ ability to provide industrial companies with a simpler supply chain, which could help them address parts shortages amid geopolitical challenges and reduce dependency on foreign suppliers providing around $12 Billion worth of investment in 3D printer manufacturers since 2011.
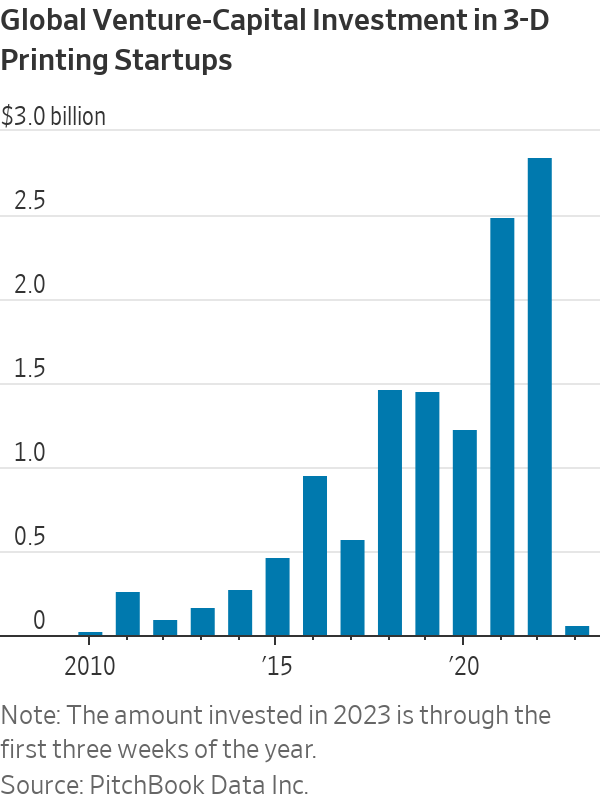
During this time the public markets were not to be outdone by private venture capital activity. Israel's Objet dropped plans for an IPO and instead merged with Stratasys in a stock deal valuing the combined companies at about $1.4 billion in 2012. Stratasys also acquired popular hobbyist 3D printer maker, MakerBot, in 2013. The two public leaders, 3D Systems (26 acquisitions) and Stratasys (10), continually acquired printing material providers and 3D design software solutions to make their printers more affordable and achieve sufficient scale to drive down costs. After going public, Desktop Metal acquired ExOne to “extend Desktop Metal’s product platforms with complementary solutions” in November 2021. Not to be left out, Nano Dimension also has had a string of acquisitions since becoming public and was forced to adopt a shareholders rights plan in February to thwart activist investor Murchinson.
The Constant Inflection of 3D Printer Manufacturers
Over the last 40 years, 3D printer manufacturers have performed poorly in public markets despite promising breakthroughs in technology throughout the years. Stratasys is the only one of the four companies to make an EBITDA profit in 2022 ($6.39M) while 3D Systems remains the largest public 3D printer manufacturer with a $1.25 Billion market capitalization as of the market close on June 6th.
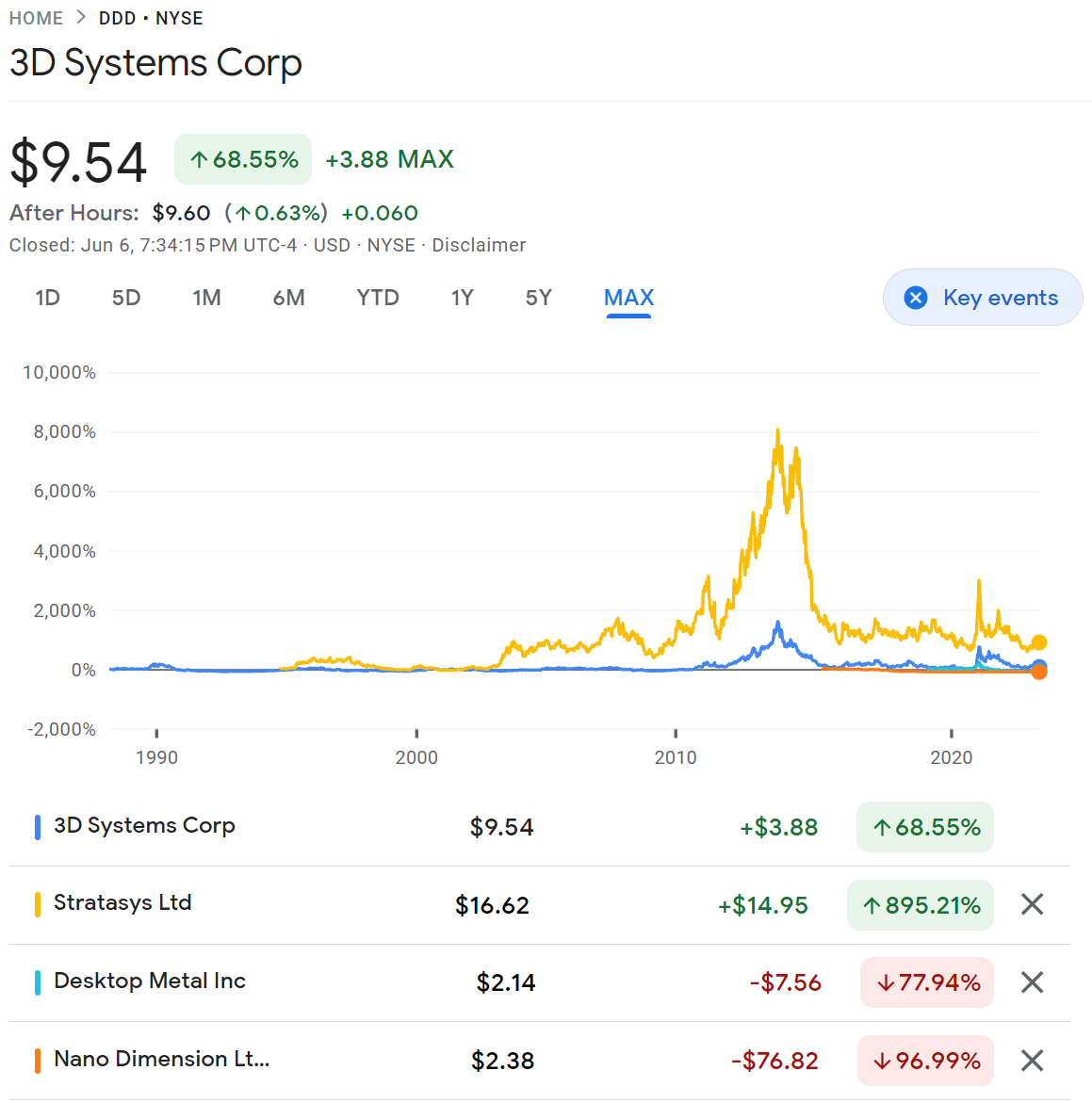
The fatal flaw in making money as a 3D-printer manufacturer is the uncompetitive cost per part as compared with other manufacturing methods such as molding (injection molding) and subtractive (CNC machining). While there are some applications where 3D printing is the only way to manufacture a certain component, those applications remain niche and low-volume.
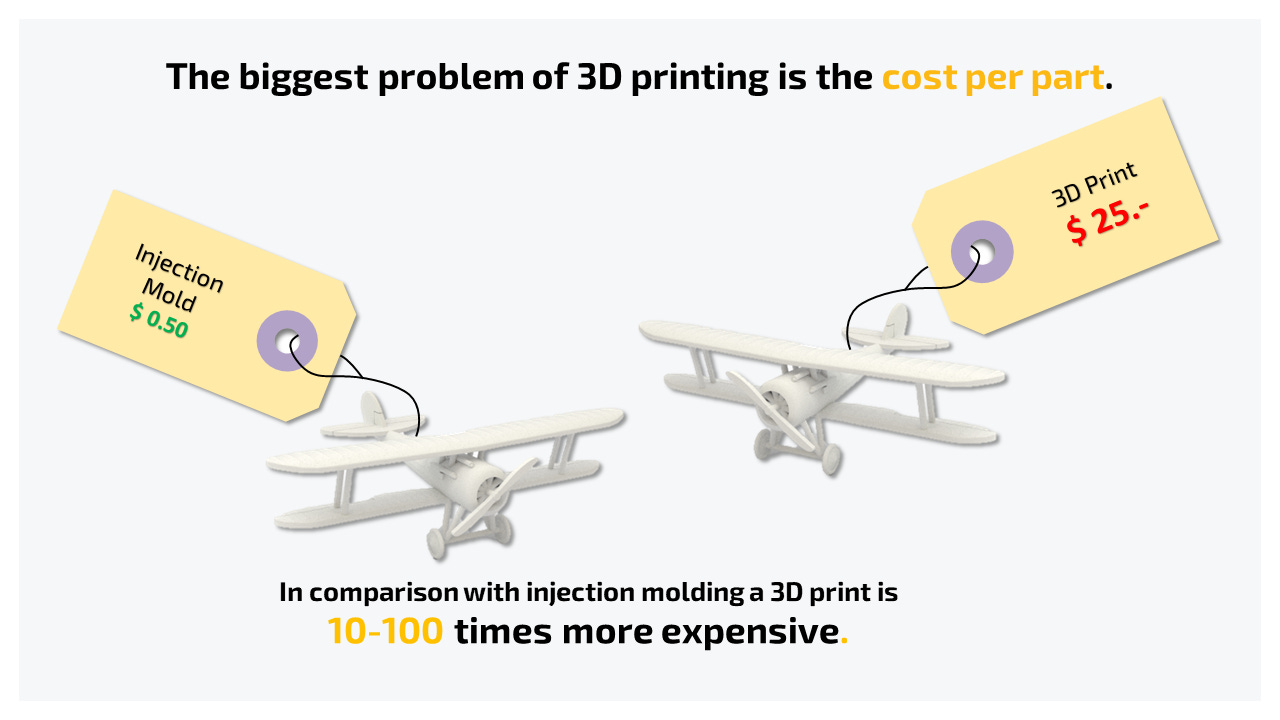
Ultimately, only low-quantity runs make unit economic sense for additive manufacturing. This leads to printer manufacturers having to consistently push into non-synergistic end markets in search of revenue growth.
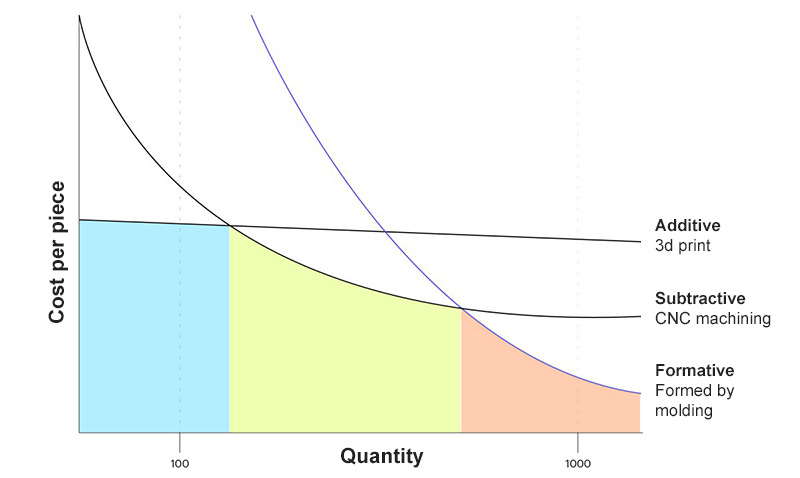
The only hope for these companies is through continual mergers to drive down fixed costs until printing technology enables a distinct declining per-unit cost curve. If a 3D-printer manufacturer can achieve scale in a subset of end markets, the costs of the printer, raw materials, and ease of use (labor productivity) could be competitive with other middle-quantity manufacturing methods. Until then, get your 🍿 ready and enjoy the M&A drama.
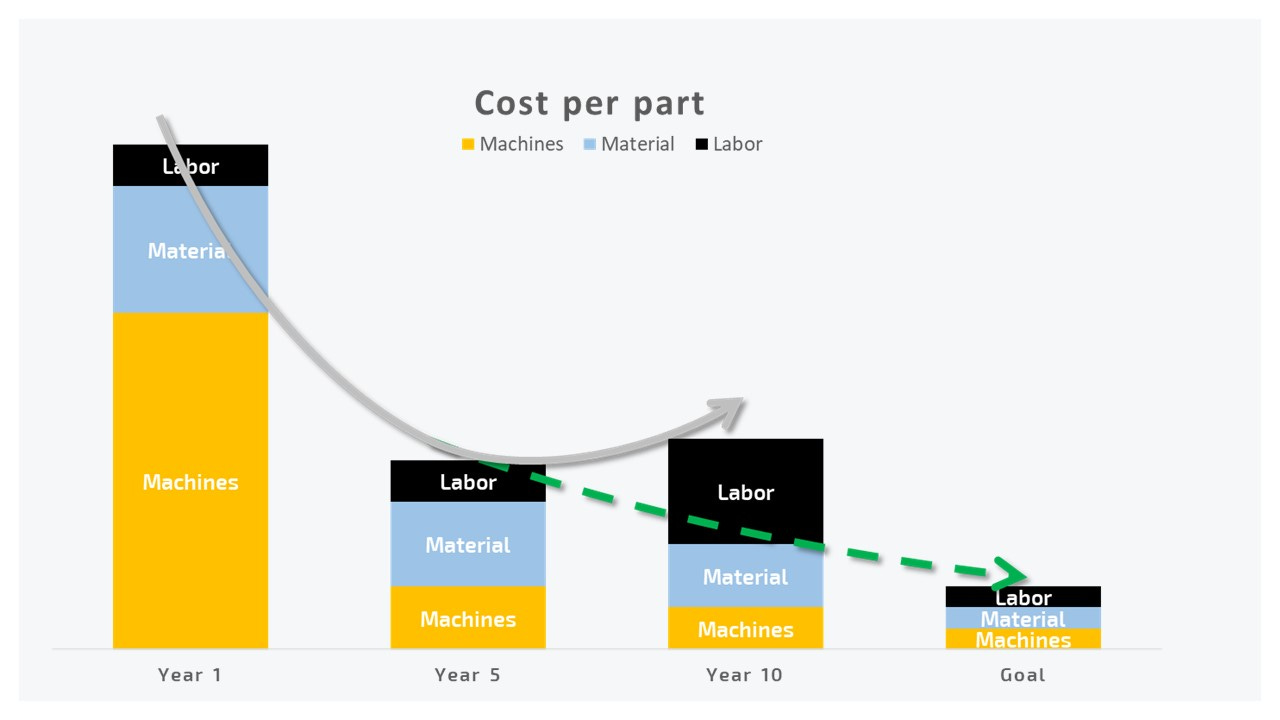
Where to Follow for Future Developments
TCT Magazine, 3Dprint.com, and IndustryWeek have ongoing coverage of the 3D Nano Desktop Stratasystems saga. Exponential Industry will keep you informed during our weekly digest.
Update June 18th, 2023
From The additive manufacturing cost per part challenge, Terry Wohlers, Industry consultant & President, Wohlers Associates:
People often asked about the most significant challenges the AM industry faces. At or near the top of the list is the cost of machines and materials. The price-to-performance ratio of AM products continues to improve, but it is far from where it needs to be. One possible solution to the price of machines is to improve build speed. If speed improves by 2x, you can build twice as many parts in a given period of time. This spreads the machine depreciation cost over these parts, which reduces the cost per part. Imagine this cost reduction if a machine is 3-5x faster. The price of materials needs to decline dramatically before adoption becomes mainstream among manufacturing companies. Some materials are priced orders of magnitude higher than similar materials for conventional manufacturing processes. This is mostly acceptable for prototyping and tooling quantities but becomes a “showstopper” when scaling to production volumes. AM must create value. If it does not, companies cannot justify its use. Consolidating two or more parts into one, reducing material and weight, and improving a product’s performance are design methods that can help create value. This, along with a reduction in the price of machines and materials and improvement in build speed, will lead to a greater adoption of AM for production applications.
I doubt if any of these mergers happen that it will help the cost curve any time soon.
The process of integrating varying business units, finding and dealing with duplication of effort/roles on top of some hostile cultural differences between the various companies is going to take years to resolve, that will inevitably slow them down, making space for competition to move faster to meet customer needs.
Part cost comparisons to other manufacturing methods typically mean you should use another method unless you are doing a short run.
There are plenty of shorter run applications in manufacturing that do not have the same razor thin margins as mass production.
Reducing the cost of producing parts with AM should lead to a broader range of viable applications, but not necessarily mass production in the millions.